**Product Details:**
- **Model No.:** S-139
- **Approximate Size:** 60mm x 30mm
- **Surface Roughness:** 3.2 Ra
- **Trademark:** S-Bright
- **Transport Package:** Carton (as per your requirement)
- **Specification:** Customized
- **Origin:** Dongguan, China
- **HS Code:** 72286000
---
**OEM Customized Precision Polished Aluminum 6061 CNC Machining Part for Automotive Billet Hose Separators (S-139)**
**Application:** Machinery, Appliances, Optoelectronics, Digital Electronics, Medical Packaging Instruments, Automobiles, Motorcycles, Bicycles, etc.
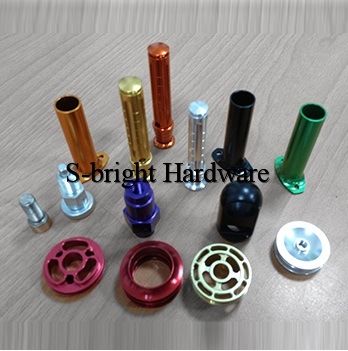
**Machining Capabilities:**
- Swiss Turning
- CNC Turning & Chucking
- CNC Lathing
- CNC Milling
- Honing
- Grinding
- Secondary Machining
- Brazing
- Soldering
- Magnafluxing
- Bending
- Slotting
- Knurling
- Threading
- Crimping
- Assembly
- Heat Treating
- Plating
- Zone Annealing
- Wire EDM Cutting
**Processing Size:**
- Maximum Processing Diameter: 150mm
- Maximum Processing Length: 300mm
- Maximum Processing Depth: 120mm
- Surface Roughness: Ra 0.3um
- Machining Tolerance: ±0.007mm
- Applied Software: Pro/E, AutoCAD, SolidWorks, IGS, UG, CAD/CAM/CAE
**Packing Material:** Eco-friendly PP bag, EPE foam, carton box, wooden box, paper, blister film, bubble film, plastic web, anti-corrosion bags, etc.
**Sample Delivery Time:** 7–14 days
**Mass Production Delivery Time:** 30 days (negotiable based on order quantity)
We manufacture parts according to customer drawings in 2D (PDF format) or 3D CAD files. We accept orders with specifications such as material type, hardness, surface roughness, and finish. ODM and OEM parts are welcome!
**Materials Used:**
- **Stainless Steel:** AISI 303, 304, 316, 316L, 430F, 440C, 630
- **Aluminum:** ASTM 380, 2017, 2011, 2024, 5051, 5052, 5056, 6013, 6061, 6063, 6082, 7075, ADC10 (AISi8Cu3), Extruded/Extrusion Aluminum
- **Carbon and Alloy Steel:** AISI 1008, 1010, 1015, 1025, 1030, 1045, 1060, 12L14, 1144, 1215, 4140, 4340, SCM440
- **Brass:** CA260, C36000, C3601, C3602, C3603, C3604, C37700, C3771, Hpb59-1, H62, C27200 (CuZn37), etc.
- **Plastic:** POM, Nylon, Noryl, Acetal, Delrin, Polycarbonate, PEEK, Acrylic, ABS, Bakelite
- **Special Materials:** Titanium 6AL-4V, Carpenter Invar 36, Remko B, Nickel Silver C79200, ASM 4640 (Aluminum Bronze), Hastelloy C276 Nickel Alloy
**Finishes Offered:**
- Nickel Plating / Electroless Nickel / Zinc Plated / Hard Chrome Plating
- Anodizing / Hard Anodized
- Black Oxide
- Passivation
- Sand Blasting
- Laser Marking
- Powder Coating
- Chem Film
- Vacuum Deposited Aluminum (Mirror Finish) / #4 Brushed Finish / #8 Mirror Finish
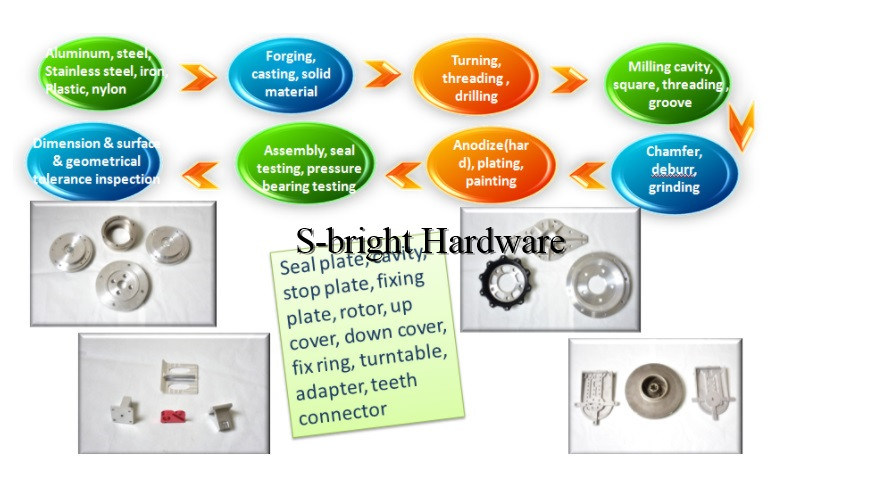
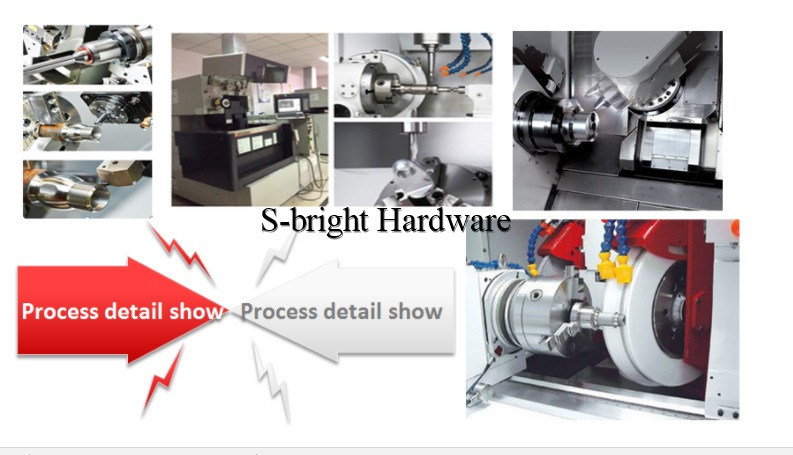
**Quality Control:**
We ensure quality through a variety of testing instruments and machines. All products undergo inspection according to customer requirements before packing.
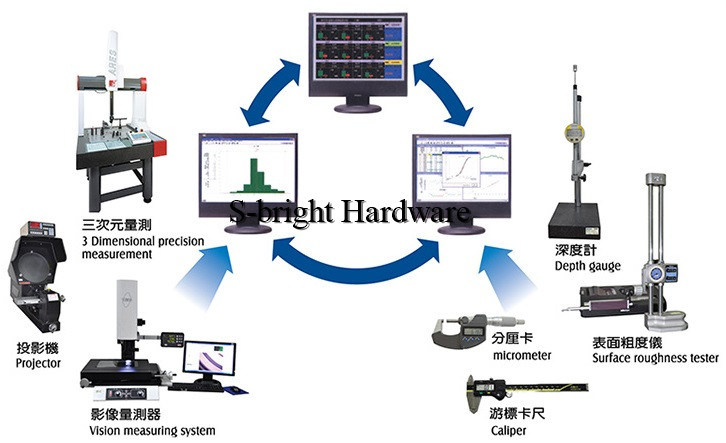
**Packaging & Shipping:**
We pack our products according to your request using various materials. We ship via courier, air, or sea.
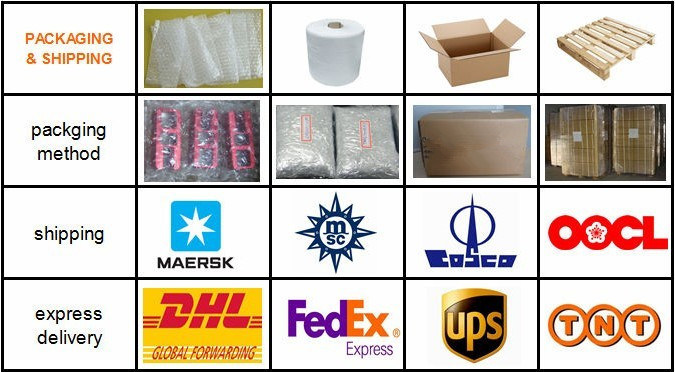
**FAQ:**
**Q: Are you a trading company or a manufacturer?**
**A:** We are a factory.
**Q: Can you supply samples? What is your sample and production lead time?**
**A:** Yes, we can offer free samples. Generally, it takes 1–2 weeks for samples, depending on the part. For mass production, it usually takes 2–4 weeks, negotiable based on order quantity.
**Q: How can I track my order without visiting your company?**
**A:** We will provide a detailed production schedule and send weekly reports to keep you updated.
**Q: How do you manage quality?**
**A:** We are ISO-certified. We have an effective in-process quality control system in place. If you need more details, feel free to contact us.
**Q: How do you provide pricing?**
**A:** We quote prices based on your design, material, and finish, and offer the best price possible.
**Q: What are your payment terms?**
**A:** We accept T/T, L/C, etc. Typically, 50% deposit and 50% balance before shipment.
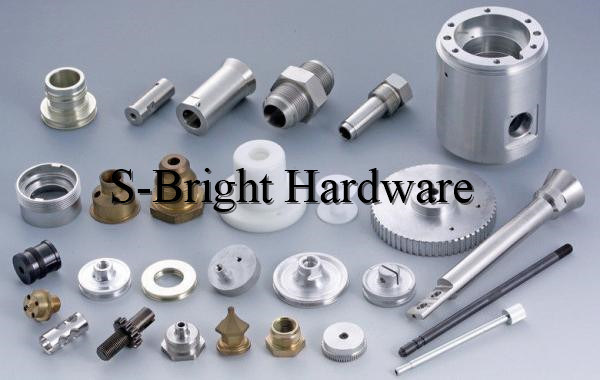
**Contact Us:**
Mr. Jack Huang
**Dongguan S-Bright Hardware Machinery Co., Ltd.**
Address: No. 8 Shengping Rd, Yangwu Cun, Dalang Town, Dongguan City, Guangdong Province, China
**Tel:** 0086-769-83002446 | **Fax:** 0086-769-83002445
**Mobile:** 0086-13058558639
**Web:** [www.s-bright.net](http://www.s-bright.net)
Induction melting system is a non-contact metal melting technology based on the principle of electromagnetic induction. It generates eddy currents in the metal raw materials in a closed container through high-frequency or medium frequency current, and heats them until the metal is melted. It is commonly used for the melting and refining of steel, non-ferrous metals and alloys. This process has become one of the important means of modern metal smelting due to its high efficiency, cleanliness, and controllability.
working principle
The key to an induction melting system lies in the induction coil, which forms a strong alternating magnetic field around the coil when high-frequency or medium frequency alternating current passes through it. Conductive metal raw materials placed in a magnetic field generate eddy currents due to electromagnetic induction effects, which generate heat through resistance and ultimately heat the metal to its melting point. Due to the self stirring effect formed by the metal melt pool itself, the melting process is uniform and efficient.
component
Induction coil: generates an alternating magnetic field to heat metal.
High frequency/medium frequency power supply: Supply the required AC power.
Cooling system: Keep the coil temperature moderate to prevent overheating.
Control system: Adjust power output and monitor the melting process.
Melting crucible: accommodates and holds the metal to be melted.
Key advantages
Efficient melting: rapid heating, high energy conversion efficiency.
Uniform melting: The stirring effect naturally formed in the molten pool results in uniform composition.
Clean and environmentally friendly: Closed systems reduce pollutant emissions.
Energy saving and consumption reduction: saves energy compared to traditional methods.
High degree of automation: easy to achieve continuous production and reduce labor demand.
application area
Induction melting systems are widely used in metal processing and manufacturing industries
Steel industry: producing various types of steel and steel grades.
Nonferrous metals: melting of aluminum, copper, zinc, etc.
Precision casting: Preparation of high-quality alloys.
Gemstone processing: melting and refining of gold and silver.
Scientific research: Preparation of metal samples in the laboratory.
Development Trend svacuum induction melting
With the innovation of materials science and power electronics technology, induction melting systems are moving towards intelligence and greenness. Using a higher frequency power supply to improve melting rate and purity; Through data collection and analysis, achieve optimized control of the smelting process; Develop environmentally friendly fluxes and high-temperature resistant materials to further reduce energy consumption and environmental impact. At the same time, induction melting equipment is also developing towards modularity and miniaturization to meet the needs of more segmented markets.
Vacuum induction melting, melting gold, medium frequency melting, induction melting, melting furnace,
Ningbo Dedao Electronic Technology Co., Ltd , https://www.nbdedao.com