**Product Details:**
- **Model No.:** S-139
- **Approximate Size:** 60mm * 30mm
- **Surface Roughness:** 3.2
- **Trademark:** S-Bright
- **Transport Package:** Carton (as per your requirement)
- **Specification:** Customized
- **Origin:** Dongguan, China
- **HS Code:** 72286000
---
**OEM Customized Precision Polished Aluminum 6061 CNC Machining Part for Automotive Billet Hose Separators (S-139)**
**Application:** Machinery, Appliances, Optoelectronics, Digital Electronics, Medical Packaging Instruments, Automobiles, Motorcycles, Bicycles, and more.
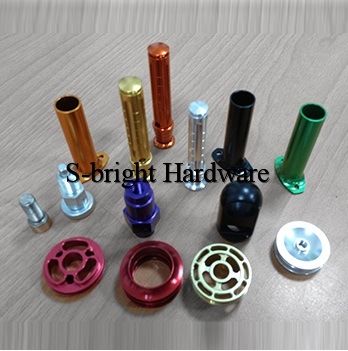
**Machining Capabilities & Surface Finish:**
- Swiss Turning
- CNC Turning & Chucking
- CNC Lathing
- CNC Milling
- Honing
- Grinding
- Secondary Machining
- Brazing
- Soldering
- Magnafluxing
- Bending
- Slotting
- Knurling
- Threading
- Crimping
- Assembly
- Heat Treating
- Plating
- Zone Annealing
- Wire EDM Cutting
**Processing Sizes:**
- Maximum Processing Diameter: 150mm
- Maximum Processing Length: 300mm
- Maximum Processing Depth: 120mm
- Surface Roughness: Ra 0.3µm
- Machining Tolerance: ±0.007mm
- Applied Software: Pro/E, AutoCAD, SolidWorks, IGS, UG, CAD/CAM/CAE
**Packing Materials (as per customer request):** Eco-friendly PP bag, EPE foam, carton box, wooden box, paper, blister film, bubble film, plastic web, anti-corrosion bags, etc.
**Delivery Time:**
- Trial Sample: 7–14 days
- Mass Production: 30 days (negotiable based on order quantity)
We produce parts according to customer drawings in 2D (PDF format) or 3D CAD files, specifying the order quantity, material, hardness, surface roughness, and finish. ODM and OEM parts are welcome!
**Materials We Use:**
- **Stainless Steel:** AISI 303, 304, 316, 316L, 430F, 440C, 630
- **Aluminum:** ASTM 380, 2017, 2011, 2024, 5051, 5052, 5056, 6013, 6061, 6063, 6082, 7075, ADC10 (AISi8Cu3), Extruded/Extrusion Aluminum
- **Carbon & Alloy Steel:** AISI 1008, 1010, 1015, 1025, 1030, 1045, 1060, 12L14, 1144, 1215, 4140, 4340, SCM440
- **Brass:** CA260, C36000, C3601, C3602, C3603, C3604, C37700, C3771, Hpb59-1, H62, C27200 (CuZn37), etc.
- **Plastic:** POM, NYLON, NORYL, Acetal, Delrin, Polycarbonate, PEEK, Acrylic, ABS, Bakelite
- **Special Material:** Titanium 6AL-4V, Carpenter Invar 36, Remko B, Nickel Silver C79200, ASM 4640 (Aluminum Bronze), Hastelloy C276 Nickel Alloy
**Finishes Available:**
- Nickel Plating / Electroless Nickel / Zinc Plated / Hard Chrome Plating
- Anodizing / Hard Anodized
- Black Oxide
- Passivation
- Sand Blasting
- Laser Marking
- Powder Coating
- Chem Film
- Vacuum Deposited Aluminum (Mirror Finish) / #4 Brushed Finish / #8 Mirror Finish
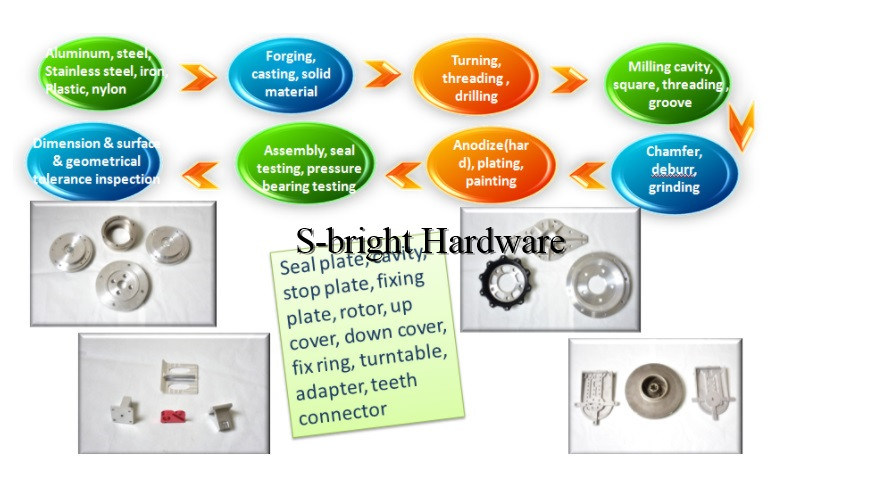
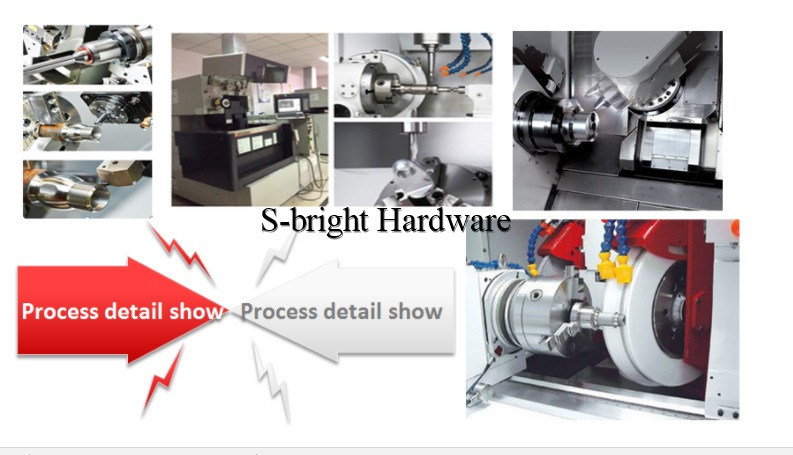
**Quality Control:**
We ensure high-quality products using various testing instruments and machines. All items are inspected according to customer requirements before packaging.
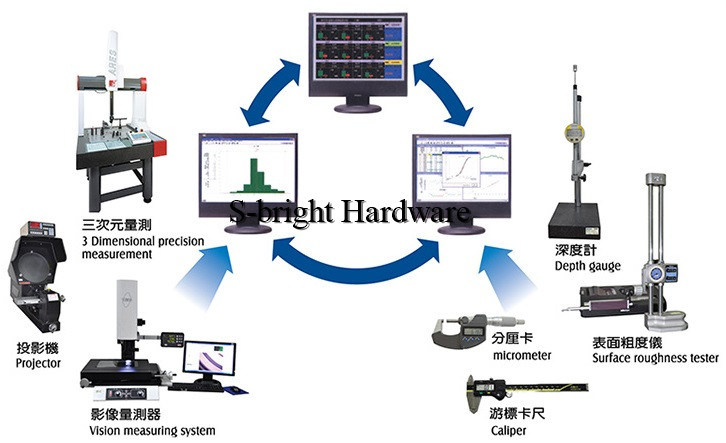
**Packaging & Shipping:**
We pack products according to customer requests using different materials. We ship via courier, air, or sea.
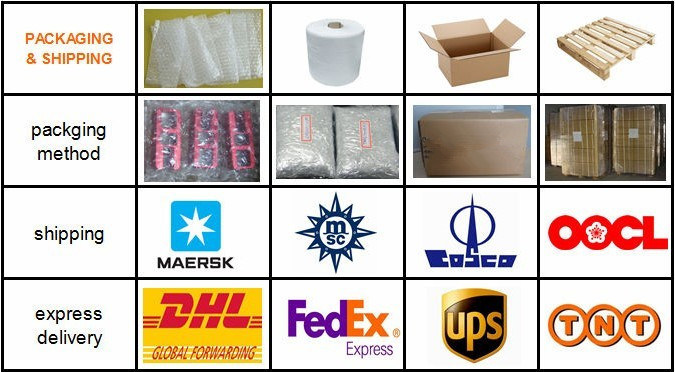
**FAQ:**
Q: Are you a trading company or a manufacturer?
A: We are a factory.
Q: Do you offer samples? How long is the sample and production lead time?
A: Yes, we can provide free samples. Typically, it takes 1–2 weeks for samples and 2–4 weeks for mass production, depending on the order quantity.
Q: How can I track the progress of my order without visiting your company?
A: We will provide a detailed production schedule and send weekly reports to keep you updated.
Q: How do you manage quality?
A: We are ISO-certified and have an effective in-process quality control system.
Q: How do you provide pricing?
A: We quote prices based on your design, material, and finish.
Q: What are your payment terms?
A: We accept T/T, L/C, etc. Usually, 50% deposit and 50% balance before shipment.
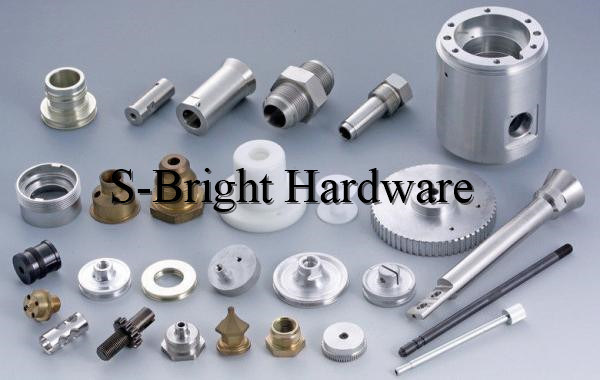
**Contact Us:**
Mr. Jack Huang
Dongguan S-Bright Hardware Machinery Co., Ltd.
Address: No.8 Shengping Rd, Yangwu Cun, Dalang Town, Dongguan City, Guangdong Province, China
Tel: +86-769-83002446 | Fax: +86-769-83002445
Mobile: +86-13058558639
Web: www.s-bright.net
Induction heat treatment system is an advanced metal material heat treatment process that uses the principle of electromagnetic induction to heat metal materials, changing their microstructure and improving their physical and mechanical properties. This system is widely used in multiple industries such as steel, aviation, automotive, and machinery manufacturing, and plays an irreplaceable role in improving material hardness, wear resistance, toughness, and other aspects.
working principle
The core of induction heat treatment system lies in electromagnetic induction heating. When an alternating current passes through an induction coil, an alternating magnetic field is generated around the coil. Metal workpieces placed near the coil will generate eddy currents, known as induced currents, under the action of this magnetic field. When this current flows inside the workpiece, it generates heat, causing the workpiece to be heated. By controlling the current frequency, power, heating time, and cooling method, it is possible to accurately perform heat treatment on the workpiece, such as surface quenching, tempering, annealing, normalizing, etc.
system composition
A complete induction heat treatment system mainly includes the following parts:
Induction heater: generates an alternating magnetic field to heat the workpiece.
Power supply: Provides electrical support for induction heaters.
Control system: Monitor and adjust various parameters of the heating process to ensure the effectiveness of heat treatment.
Cooling system: used to control the cooling rate of the heated workpiece and complete the heat treatment cycle.
Fixture: Fix the workpiece to the optimal heating position.
Characteristics and advantages
1. Precise control: By precisely adjusting parameters such as current and frequency, precise control of heating depth and temperature can be achieved.
2. Efficient and fast: Induction heating has a fast speed and can heat up to the desired temperature in a very short time, shortening the heat treatment cycle.
3. Energy saving and environmental protection: There is no open flame during the heating process, which saves a lot of energy compared to traditional furnaces, and there are no harmful substance emissions.
4. Local heating: It can heat specific parts of the component to avoid resource waste and deformation caused by overall heating.
Application Cases
Automotive manufacturing: used for surface quenching of components such as gears, connecting rods, crankshafts, etc., to improve their hardness and wear resistance.
Aerospace: Heat treatment of key components such as aircraft landing gear and engine blades to enhance their fatigue resistance.
Mechanical manufacturing: Quenching treatment of cutting tools, molds, etc. to extend their service life.
Oil extraction: Heat treatment of parts such as drill bits and pipeline joints to improve corrosion resistance and mechanical strength.
conclusion
Induction heat treatment systems play an indispensable role in modern industry through their efficient heating capacity and precise control mechanism. With the continuous advancement of technology, induction heat treatment systems are developing towards smarter and more energy-efficient directions, and more application scenarios will be developed in the future.
Induction hardening, heating equipment, quenching equipment,, induction heating
Ningbo Dedao Electronic Technology Co., Ltd , https://www.nbdedao.com