[New weather after year, cutting machine through the bottom price. The lowest price of the entire network, all kinds of custom cutting machine will be 50% discount wholesale order price, a small piece of drawings to achieve a three-dimensional 3D cutting machine parts, where to set where, customers no longer have to worry about no supply and reserve price . What are you waiting for? The reserve price is known to you. You haven't asked if the inquiry is low. For details, please contact the official website of China Cutter Trading Co., Ltd., Tel: :/ Reference: Cutting Machine
In the past two years in China, with the increase in labor costs, the price advantage of the export of middle and low-end CNC machine tools will gradually be lost, and the export volume will surely decrease. If the machine tool companies continue to focus on the production of traditional standard cutting machine tools, the sales volume will gradually shrink, and there will be no future development. Therefore, China's cutting machine tools must change their concepts, vigorously develop efficient production of advanced CNC cutting machine tools, use domestically-made high-efficiency advanced machine tools to replace foreign products, recapture this part of the market occupied by imported cutting machine tools, and pay attention to after-sales production services. Only in this way, our country’s CNC cutting machine tool companies have a promising future, and China's CNC cutting machine tool industry can be rejuvenated.
The general situation of the machinery manufacturing industry In recent years, China's manufacturing industry has achieved sustained high-speed development. China has become a manufacturing country: all countries in the world are importing a large number of Chinese products, and China's exports, CNC cutting machine tool products have accounted for the majority. In the current economic cold wave and crisis, although the machinery industry has been greatly affected, the total size and total output are second only to the United States, surpassing Japan, ranking second in the world, and exports have surpassed Germany to reach the top position in the world. 2009 China Car production has surpassed the United States and ranks first in the world. China has become a world-famous manufacturing power. China ranks third in the “Top 10 Manufacturing Powerhouses in the World†list published in the 2010 Global Manufacturing White Paper. In this year's "World Machinery 500", the United States ranked first with 126 companies, Japan ranked second with 124 households, and China was ranked third in the country. However, none of China’s top ten machinery companies in the world’s top 500 machinery companies was selected this year; of the world’s top 100 machinery manufacturers, only nine were selected. It should be recognized that China’s manufacturing industry is large and not strong. Although it is a manufacturing country, it cannot be called a manufacturing power. For example, steel, we export a lot of low-cost steel and import high-value alloy steel. The machine tool is also exporting cheap mid-to-high-end machine tools, while importing expensive CNC and precision machine tools.
In recent years, although there is no small development in the CNC cutting machine tool industry, it is far behind the development of the machine tool industry. Most of the highly efficient cutting machine tools used in production are imported from abroad (including cutting machine tools produced by foreign companies in China). We are also exporting a lot of cutting machine tools, but mainly low-cost standard cutting machines. In 2004, about 2.5 billion pieces of cutting machine tools were produced in China, of which 2 billion pieces were cheap and low-grade cutting machine tools (most of which were exported). In the following years, exports were still basically medium and low-grade cutting machine tools. In the US market, medium-sized twist drills cost about US$10 each, while the low-end twist drills produced in China on the market are priced at just US$1 and used as handcrafts. China now has the world's largest automotive industry, but the high-efficiency production lines introduced by the automotive industry from abroad have used 80% to 90% of the cutting machine tools, which are still imported cutting machine tools (including domestic foreign-funded enterprises). Now China's cutting machine tool supply and marketing situation is that high-end advanced cutting machine tool products mainly rely on imports from abroad, and low-grade cutting machine tools malignant expansion (mostly exports), this situation must be changed as soon as possible. China's machinery manufacturing industry uses a large number of standard cutting machine tools, while developed countries are using a large number of efficient cutting machine tools, resulting in China's processing efficiency is far lower than foreign. CNC cutting machine tool factory in China is still mass production of traditional standard cutting machine tools, some small factories also produce a large number of low-grade cutting machine tools, according to statistics, China consumes 40% of the world's materials, sales revenue only accounted for 12% to 15% of the world's industry. Gross margins of foreign companies are all around 40%, while the profits of Chinese factories are low, and some factories are still losing money. Now our country's factory mainly produces traditional standard cutting machine tools. Judging from the technological development trend of the machinery manufacturing industry, the proportion of high-efficiency CNC machine tools in China's factories will increase year by year. The demand for efficient cutting machine tools will increase rapidly, while the demand for traditional standard cutting machine tools will decrease year by year.
The labor productivity of China's manufacturing industry is only 1/3 to 1/5 of that of the United States and Japan. Many Chinese machinery products are cheap but their quality is also low. Recently, due to the appreciation of the renminbi and the rapid increase in domestic labor costs, coupled with the economic cold wave and crisis, it has seriously affected the export of middle and low-end products, and forced us to improve the technological level of the machinery industry as soon as possible, change the crisis into an opportunity, and forge ahead into a manufacturing powerhouse. . From 2000 to 2008, the rapid development of China's machinery manufacturing industry from 2000 to 2008, the development of China's machinery manufacturing industry is extremely rapid, not only the production of automobiles, machine tools, shipbuilding, power generation equipment, etc., has grown rapidly, but also the product level has been continuously improved. The market share of domestic machine tool output value was 56.3% in 2007 and 61% in 2008. It continued to increase in 2009, reaching 70.1%. In 2008, China's machine tool industry consumed 19.44 billion U.S. dollars worth of machine tools, ranking first in the world; 13.96 billion U.S. dollars worth of machine tools, ranking third in the world; 2.11 billion U.S. dollars worth of export machine tools, ranking sixth in the world; and 7.59 billion U.S. dollars worth of imported machine tools, ranking first in the world. Import and export of machine tools exceeded US$5.48 billion. In 2009, affected by the cold wave of the world economy, the growth rate was reduced, but foreign countries were more affected. Last year, China’s production machine tools leapt to the top in the world with 5.9 billion U.S. dollars in machine tools, 1.14 billion U.S. dollars in machine tools, and 4.49 billion U.S. dollars in machine tool imports and exports. Machine tools for import and consumption ranked first in the world for eight consecutive years. In 2007, the output of CNC machine tools in China was 123,257 sets, an increase of 32.6% over 2006. In 2008, China's CNC machine tools were affected by the world economic crisis, and the output was 122,211 units, which was basically the same as in 2007. From January to December of 2008, the output of CNC machine tools in China was affected by the economic crisis. After July, the output declined, and it recovered slightly in December. In 2009, the output of CNC machine tools in China increased significantly to 143,904 units, and the market share of domestic CNC machine tools reached 62%. The situation of China's machinery manufacturing industry in 2009 From the perspective of the general environment, since the second half of 2008, the machinery manufacturing industries in various countries have been affected by the financial crisis to varying degrees, and the losses of several major automobile and machine tool producing countries have been particularly severe. The production of automobiles in all countries in the world has dropped significantly. China's auto production and sales have not only declined, but have continued to increase dramatically. In 2009, China’s auto production surpassed the United States and ranked first in the world. In the first half of 2009, the statistics of machine tool production in major countries were as follows: In the first quarter of 2009, the Japanese machine tool industry's orders fell by 84.6%. Domestic demand and exports both fell, which affected the sales decline by 46.2%.
US machine tool orders began to decline from November 2008. New orders received in April 2009 were only US$97.04 million, a decrease of 42% from March 2009 and 78% from April 2008. Orders from January to April 2009 were comparable year-on-year. 71% reduction. Germany has revised its forecast for 2009 full-year order trends from a previous decline of 7% to a decline of 10% to 20%. The total orders for German machine tools fell by 70% year-on-year.
Compared with the same period of 2008 in China, Taiwan's machine tool exports fell by 51.9% in January-April 2009. Imports decreased by 84.6%, total exports decreased by 51.9% from the same period of last year, and exports decreased significantly. Relatively speaking, the CNC machine tool industry in China is less damaged. According to the statistics of the 177 key contact companies of the China Machine Tool Association, the total industrial output value decreased by 5.0% year-on-year from January to May 2009, and the sales revenue decreased by 6.2% year-on-year. %, cumulative total profit decreased by 33.1% year-on-year. The data shows that in the financial crisis, the Chinese machine tool industry did not suffer a major injury. Statistics show that from January to April of 2009, the total investment in fixed assets of the machine tool industry was RMB 23.2 billion, up 48.8% year-on-year; by May 2009, the machine tool industry declared 30 items included in the national revitalization planning technical reform project, with a total investment of 72.1. Billion yuan, which effectively improves the machine tool industry's manufacturing level and capabilities. In the second half of 2009, the production situation in the machine tool industry significantly improved. Due to the low base in the second half of 2008, the monthly growth rate of total industrial output value of the machine tool industry reached double digits in July 2009. The specific completion situation and the year-on-year growth rate. In the first half of 2010, the machinery manufacturing industry in the first half of 2010, China's machinery manufacturing industry is in good condition, the overall production and sales are booming, the same is true for the machine tool industry. The machine tool industry continued to grow rapidly. In the first half of this year, the total output value was 242.42 billion yuan, an increase of 41.4% year-on-year, of which the total output value of the machine tool industry was 57.21 billion yuan, a year-on-year increase of 31.7%. The output of metal cutting machine tools was 338,209 units, of which the output of CNC machine tools reached 945,191 units, a year-on-year increase of 25.8% and 52.2% respectively. The metal cutting machine tool industry achieved a profit of 2.27 billion yuan, a year-on-year increase of 68.3%. The profit margin of the output value was 5.0%, an increase of 1.1 percentage points year-on-year. In the first half of 2010, the total export value of China's machine tool industry was 3.11 billion U.S. dollars, which was a substantial increase from 2009, but it was still 7.1% lower than the same period in 2008. The investment boom driven by the domestic economic stimulus plan resulted in a significant increase in imports of machine tools. Imports in the first half of 2010 increased by 12.7% compared with the same period of 2008. Imports of cutting and cutting machine tools increased particularly rapidly, reaching US$530 million in the first half of the year, a year-on-year increase of 138.0. %.
China's exports are cheap medium and low-end machine tools, while imports are expensive CNC and precision machine tools. The current situation of international economic development is still not clear. Faced with the complex and ever-changing domestic and international situation, although the situation of China's machinery industry is good in the first half of 2011, the trend is not optimistic. Compared with the manufacturing powerhouses in China and abroad, there is still a big gap in technology. We must study and improve product quality, increase high-end products, improve the level of manufacturing technology, and strive to innovate. In the post-financial crisis era, the Chinese machine tool industry is striving to achieve a major machine tool country. The transformation to a powerful machine tool. The development of China's industry In 2005, China's consumption of cutting machine tools was approximately US$1.7 billion. In 2006, the consumption of cutting machine tools was approximately US$2 billion, of which imports of cutting machine tools were approximately US$1 billion. With the rapid development of industry in 2007, sales revenue increased by about 28%. In the first three quarters of 2008, the industry continued to develop at a high speed, with an increase of more than 20%. However, after the decline in October, the growth was still above 12%. Affected by the world economic crisis, industry continued to decline in the first half of 2009, but the overall economic situation has begun to pick up after July to August, and industry has gradually improved. If China's CNC machine tool industry is to achieve further development in 2012, it must work hard on the technology and develop more sophisticated high-quality high-tech products.
[I can't think of it. I can't do it. Change your style from now on. Opening the Chinese cutting machine trading network is equivalent to opening up your wealth road, come and click on the website now! 】
Sintering Parts:
There are similarities with the production of ceramic powder sintering technology, are, therefore, a series of powder metallurgy new technology can also be used in the preparation of ceramic materials. Because of the advantages of powder metallurgical technology, it has become the key problem to solve new materials, plays an important role in the development of new materials in powder metallurgy products. Including milling and milling which is mainly metallurgical process, and powder metallurgy products and literal agreement. It is often far beyond the category of materials and metallurgy, often across multiple studies (materials and metallurgy, machinery and Mechanical) technology. Especially the modern printing metal powder 3D, in Mechanical Engineering Cheng, CAD, reverse engineering technology, layered manufacturing technology, numerical control technology, materials science, laser technology, makes the product technology of powder metallurgy technology has become a modern comprehensive more cross discipline.
Based on different raw material,we can make Carbon Steel Sintering and Stainless Steel Sintering parts.
Advantages:
Powder metallurgy has unique chemical composition and mechanical, physical properties, and these properties can not be obtained by traditional casting method. Be made directly using porous powder metallurgy technology, semi dense or fully dense materials and products, such as oil bearing, gear, cam, a guide rod, a cutter.
(1) The process of powder metallurgy technology can minimize alloy composition segregation, eliminate thick, uneven casting organization. In the preparation of high performance rare earth permanent magnetic materials, rare earth hydrogen storage materials, rare earth luminescent materials, rare earth catalyst, high temperature superconducting materials, new metal materials (such as Al-Li alloy, heat-resistant al super alloy, alloy powder, corrosion resistance of stainless steel, high-speed steel powder, intermetallic compound high temperature structural materials) plays an important role.
(2) It can be prepared by amorphous, microcrystalline, quasicrystals, nanocrystalline and supersaturated solid solution of a series of high performance etc. The balance of materials, these materials have excellent electrical, magnetic, optical and mechanical properties.
(3) It can be easily combined with various types, give full play to the characteristics of each element of the respective materials, is a kind of high performance metal based ceramic composite material and low cost technology.
(4) It can make special structure and properties of the production that ordinary smelting method can`t produce, such as a new type of porous biomaterials, porous membrane material, structure and function of high performance ceramic abrasive material.
(5) It can realize near net forming and automatic batch production, which can effectively reduce the production of resources and energy consumption
(6) It can make full use of ore tailings, steelmaking sludge, mill scale, scrap metal recycling as raw materials, is a kind of new technology can be effective and comprehensive utilization of renewable materials.
Manufacturing process:
(1) The production of powder. It includes powder preparation, mixing and other steps. For powder molding and plasticity improve powder usually add oil, rubber or paraffin as plasticizer.
(2) Pressing powder. Under the pressure of 15-600mpa, pressed into the desired shape;
(3) High temperature sintering furnace or vacuum furnace. In a protective atmosphere in sintering. Unlike metal melting, sintering at least one element is in solid state. The sintering process of powder particles by diffusion, recrystallization, welding, chemical, physical and chemical dissolution process of a series, as metallurgy products have a certain porosity.
(4) Postprocessing. In general, good Sintering Parts can be used directly. But for some high precision size requirements and has high hardness and wear resistance of the parts but also for sintering postprocessing. Postprocessing including precision pressing, rolling, extrusion, quenching, quenching, oil, And infiltration, etc.
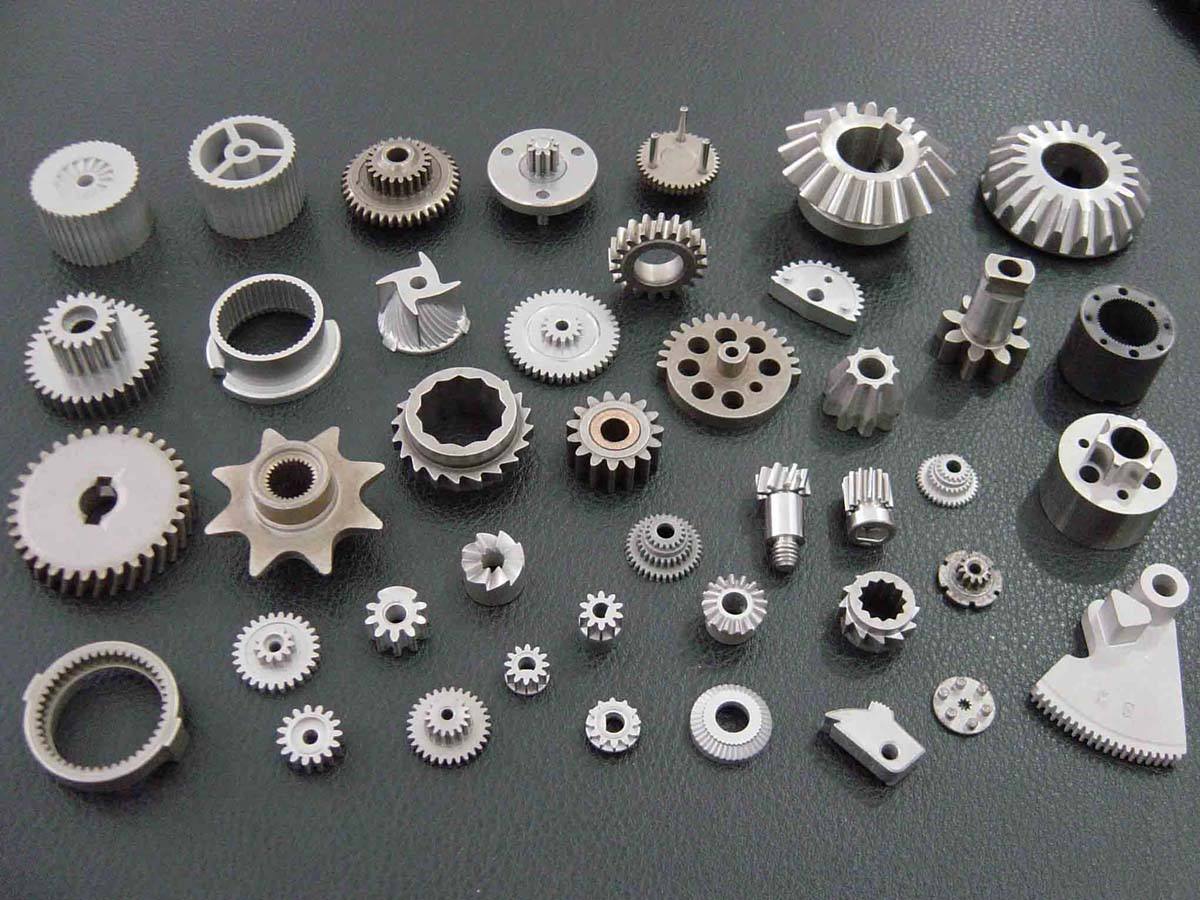
Sintering Parts
Sintering Parts,Carbon Steel Sintering,Stainless Steel Sintering,High Performance Sintering Parts
VESTA Motoring Ltd , http://www.vesta-industry.com