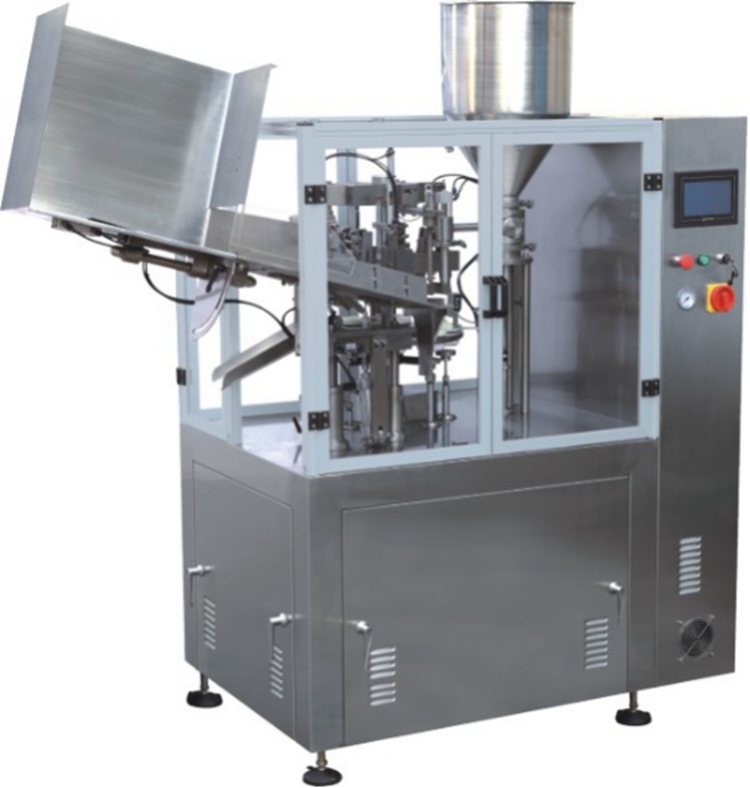
Application:
This machine is designed to fill and seal a wide range of products such as ointments, creams, lotions, toothpaste, jams, and other viscous materials. It can handle aluminum tubes, plastic tubes, and laminated tubes with ease. The machine automatically performs functions like sealing, tail folding, batch number embossing (including the manufacturing date), and more. This makes it ideal for businesses that use both plastic and aluminum tubes, as no mold changes are required, saving time and reducing errors.
Sample Tubes:
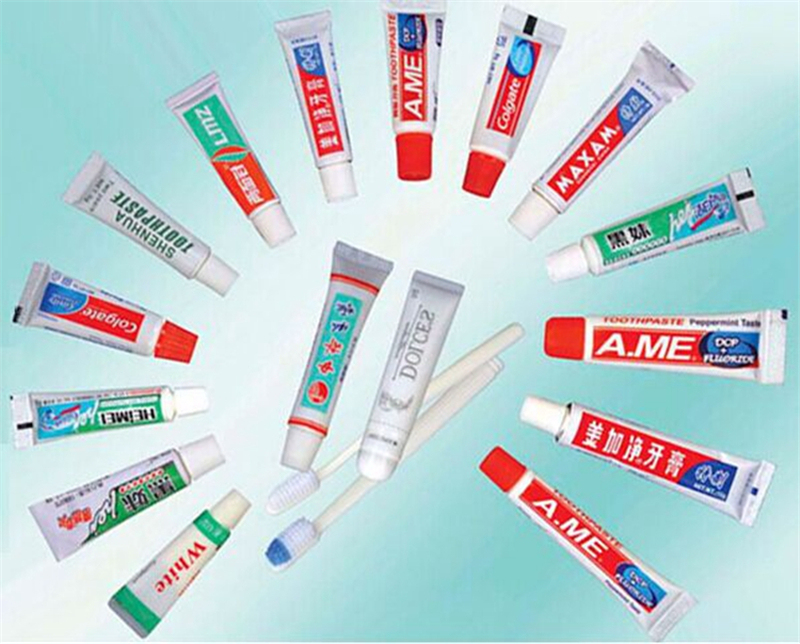
Working Principle:
The tube filling and sealing machine is designed for filling and sealing aluminum, plastic, and laminated tubes used in cosmetics, pharmaceuticals, food, and adhesive industries. The process involves several steps: tubes are fed into the machine one by one, marked and inspected, cleaned if needed, filled, sealed (or folded), batch numbers printed, cooled, cut, and finally discharged as finished products. The machine features a main transmission system, feeding mechanism, rotation unit, tail sealing system, filling system, and an electrical control system.
Key Features:
- Equipped with 9 stations and a manipulator, this machine can handle various types of tube sealing and tail folding requirements for aluminum, plastic, and laminated tubes, making it highly versatile.
- The entire process from tube feeding to marking, cleaning, filling, sealing, printing, and discharging is fully automated.
- Servo control allows precise adjustment of filling volume through a touch screen interface.
- The height of the tube chamber can be easily adjusted using a motor, and an external reverse feeding system ensures convenient and neat tube loading.
- The mechanical linkage photo sensor has a precision tolerance of less than 0.2mm, minimizing color deviation between the tube and the marking.
- Integrated control using photoelectric, electric, and pneumatic systems ensures safety and efficiency. The machine will stop automatically if there's a tube error or if the safety door is opened.
- A three-layer jacket instant heater prevents damage to the tube’s outer pattern and ensures a firm, clean sealing effect.
- The machine includes a five-fold and three-fold manipulator, allowing dual-sided code printing, which enhances product quality and machine performance.
- High-grade liquid crystal display controller with buttons provides easy operation, including speed regulation, parameter setting, pressure instruction, and trouble display. The user interface is simple and intuitive.
Technical Parameters:
Operating Speed: 80 tubes/min (max)
Filling Volume: 5-350ml
Filling Accuracy: ≤ ±1%
Suitable Hose Length: 50-210mm
Suitable Hose Diameter: Φ10-60mm
Standard: Inclined Hose Cleaning Device
Optional: External Chiller System
Optional: Blowing Suction Hose Cleaning Device
Optional: Mezzanine Barrel Insulation Device
Optional: Large Feed Tube Device (Floor Synchronization Feeding Machine)
Optional: Shaped Sealing Device (Wavy, Arc-shaped, T-type Punching, etc.)
Optional: Multicolor Filling System
Optional: Nitrogen Device Before Filling
Optional: Automatic Control Feeding Pump
Optional: Finished Tube Output Conveyor
Order Requirements:
What speed do you need?
What type of tubes do you want to fill? Plastic, aluminum, or laminated tubes?
What size of tubes? Diameter and length?
What capacity do you need to fill?
What is your raw material?
Do you need a chiller if it's a plastic tube?
What voltage do you require? Is it 380V 50Hz 3-phase?
When do you need the machine?
Our Service:
1. We can design the machine according to your specific requirements and tailor the production process to your technology needs.
2. All machines are manufactured following GMP standards, and all welding is tested via X-ray inspection.
3. We package the machine with film and then in wooden boxes, and load it into containers with the help of our engineers.
4. Our engineers will install the machine in your production room according to your layout and test it thoroughly.
5. We offer online support, so feel free to contact us via email, phone, or Skype for any assistance.
6. We also provide spare parts in the future to ensure continued operation and maintenance.
Factory Photos:
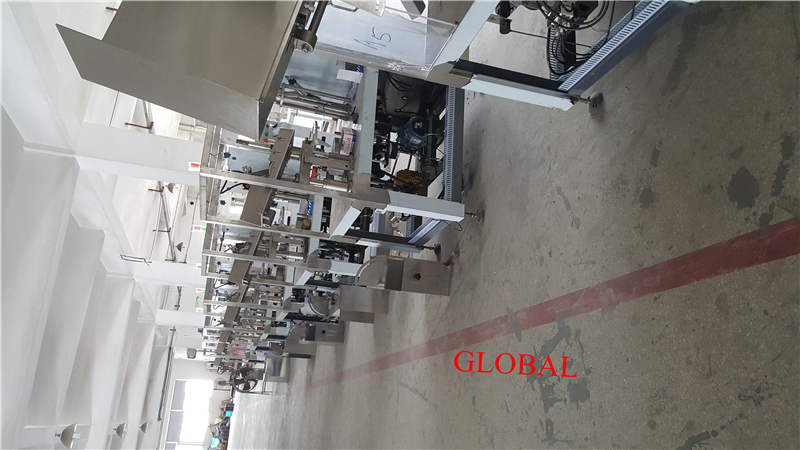
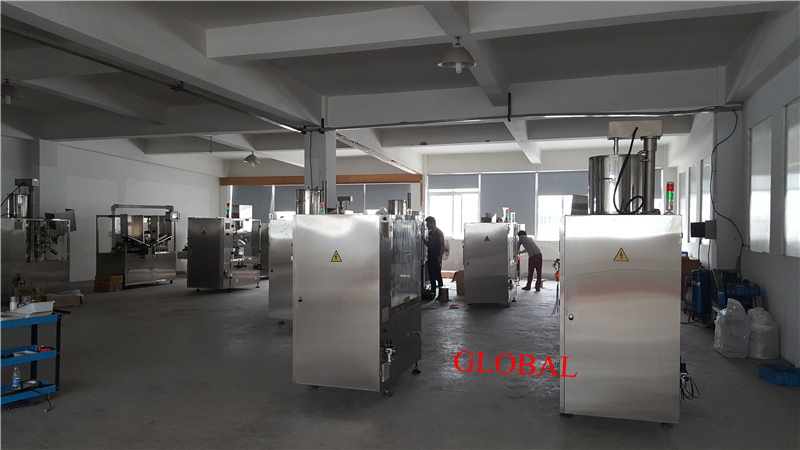
Centrifugal casting or rotocasting is a casting technique that is typically used to cast thin-walled cylinders. It is chiefly used to manufacture rotationally symmetric stock materials in standard sizes for further machining, rather than shaped parts tailored to a particular end-use.
Technical Parameters
Product Name : Bimetallic Barrel
Material: JYN3 + JYK Series Alloy
Suitable Machine: Injection / Extrusion / Blowing ...
Available Size: Φ < 500mm, L < 8,000mm
Process Method: Centrifugal Casting
Surface Hardness: 52-62 HRC
Surface Roughness: < Ra 0.8
Screw Straightness: < 0.02mm/m
Advantages
By casting and sintering high quality alloy powder on barrel inside surface with thickness1.5-2.0mm, screws can get higher performance in both wearing & corrosion resistant performance.
Application
General plastics & engineering plastics with below 70% glass fibre filling.
JYK Series Alloy
At this stage, we have JYK-1, JYK-2 and JYK-3 alloy types and treatments for wear fighting
TYPE |
COMPONENTS |
HARDNESS (HRC) |
Abrasive RESISTANCE |
Corrosion resistance |
applications |
JYK-1, C |
Fe, Cr, Ni |
56 – 60 |
x |
x |
Recycling & engineering plastics, reinforced additives less than 20%. |
JYK-2, B |
Ni, W, Cr |
58 – 62 |
xx |
xx |
Moderate corrosive, reinforced additives less than 35% |
JYK-3, D |
Ni, W, Cr |
60 – 64 |
xxx |
xx |
High abrasive and moderate corrosive plastics |
Suitability: (x good) to (xxx excellent).
TYPE |
INGREDIENTS (WEIGHT %) |
||||||||
Cr |
C |
Fe |
B |
Si |
W * |
Mn |
Ni |
Others |
|
JYK-1, C |
8 |
1.2 |
Bal |
4.3 |
4 |
/ |
0.65 |
10.8 |
< 1.0 |
JYK-2, B |
8 |
1.4 |
5 |
4 |
3.3 |
16.5 |
0.5 |
Bal |
< 1.0 |
JYK-3, D |
8 |
1.4 |
5 |
4 |
3.3 |
40 |
0.5 |
Bal |
< 1.0 |
*Highest composition of tungsten carbide can go up to 45%, which enables the barrels have 5 times wear-resistance capability than normal bimetallic barrels and up to 60% glass fibre filling in general & engineering plastics materials.
Bimetallic Barrels,Bimetallic Barrel Casting line,Extruder Bimetallic Parallel Twin Screw
Ningbo Jinyi Precision Machinery Co., Ltd. , https://www.jinyi-machinery.com