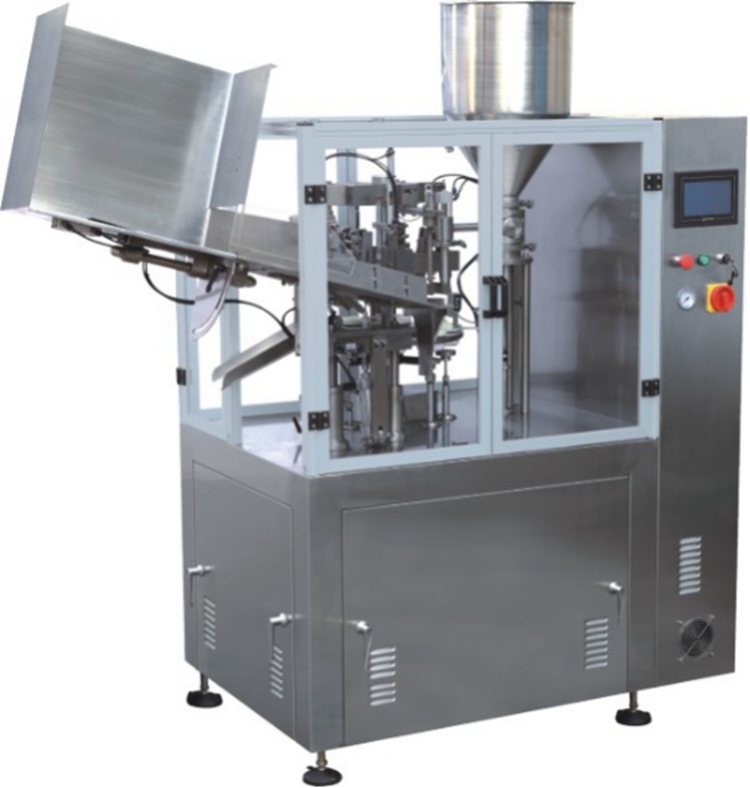
Application:
This machine is designed to fill and seal ointments, creams, jellies, toothpaste, lotions, jams, and other viscous materials in aluminum, plastic, or laminated tubes. It automatically performs sealing, tail folding, and batch number embossing (including manufacturing date). The machine can handle both plastic and aluminum tubes without requiring a mold change, making it ideal for businesses that use multiple tube types.
Sample Tubes:
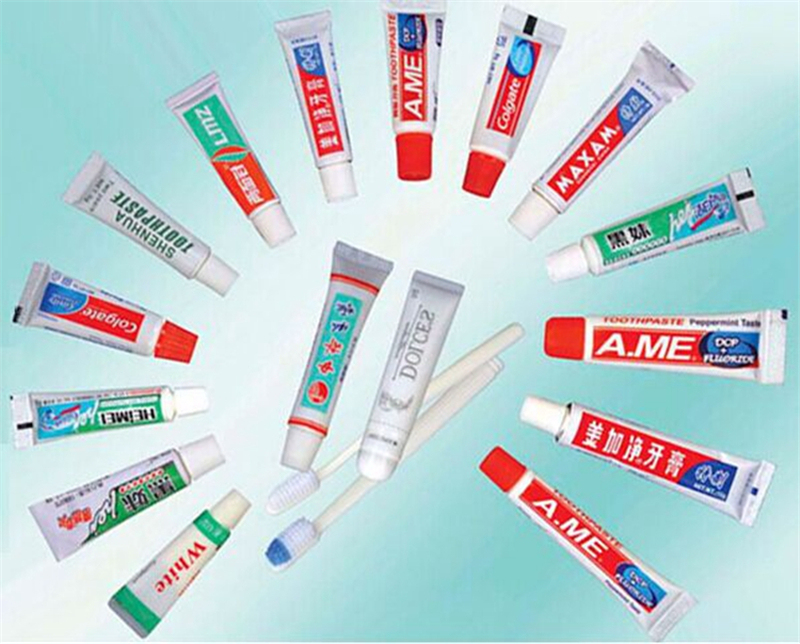
Working Principle:
The machine operates by feeding tubes into the chamber one by one. They are then transferred to the first station for marking detection, followed by tube cleaning (optional), filling, sealing, tail folding, batch number printing, cooling, cutting, and finally discharging as finished products. The system includes main transmission, feeding, rotation, tail sealing, filling, and an electrical control system.
Key Features:
- Equipped with 9 stations and a manipulator, it supports various tube types including aluminum, plastic, and laminated tubes, offering multi-purpose functionality.
- Fully automatic operation from feeding to discharging, including marking, cleaning, filling, sealing, and code printing.
- Servo control allows precise adjustment of filling volume via touch screen.
- Tube height can be adjusted easily with a motor, and the external feeding system ensures neat and efficient loading.
- High precision sensors ensure accurate alignment and reduce color deviation between the tube and marking.
- Integrated electronic, pneumatic, and photoelectric controls ensure safety and efficiency, with alarms for pressure issues and machine stoppage on errors.
- Three-layer jacket heater ensures even heating without damaging the tube’s outer surface, resulting in strong and clean seals.
- Includes a five-fold and three-fold manipulator for double-sided code printing, enhancing product quality and machine performance.
- High-grade LCD controller with buttons for easy speed control, parameter setting, and troubleshooting display, ensuring user-friendly operation.
Technical Parameters:
Operating Speed: 80 tubes/min (max)
Filling Volume: 5–350 ml
Filling Accuracy: ≤ ±1%
Suitable Hose Length: 50–210 mm
Suitable Hose Diameter: Φ10–60 mm
Standard: Inclined Hose Cleaning Device
Optional: External Chiller
Optional: Blowing/Suction Hose Cleaning Device
Optional: Mezzanine Barrel Insulation Device
Optional: Large Feed Tube Device (floor external synchronization feeding machine)
Optional: Shaped Sealing Device (wavy, arc-shaped, T-type punching)
Optional: Multicolor Filling System
Optional: Nitrogen Device Before Filling
Optional: Automatic Control Feeding Device (pump)
Optional: Finished Tube Output Conveyor
Order Requirements:
What speed do you need?
What type of tubes will you fill? Plastic, aluminum, or laminated?
What are the dimensions of the tubes? Diameter and length?
What capacity do you want to fill?
What is your raw material?
Do you need a chiller if using plastic tubes?
What voltage is required? Is it 380V, 50Hz, 3-phase?
When do you need it delivered?
Our Service:
1. We can customize the machine based on your requirements and production process.
2. All machines are manufactured according to GMP standards, with X-ray testing on all welds.
3. We pack the machine in film and wooden boxes, and load it onto containers with the help of our engineers.
4. Our engineers will install the machine in your facility and test it before handover.
5. We offer online support via email, phone, or Skype for any questions you may have.
6. We also provide spare parts in the future to ensure long-term service.
Factory Photos:
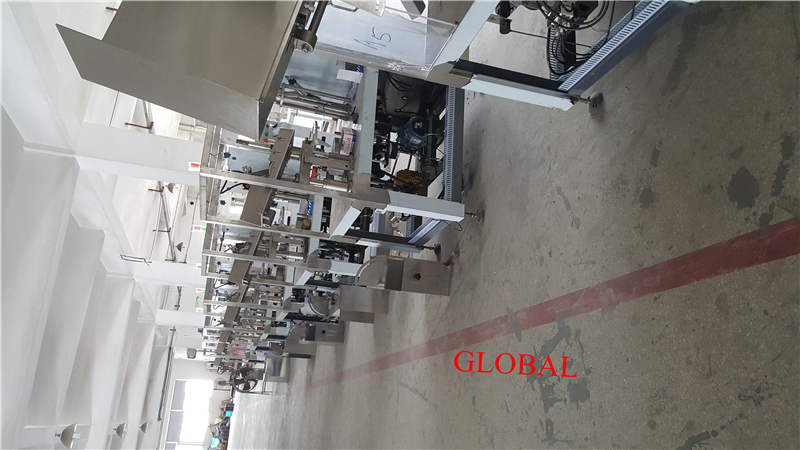
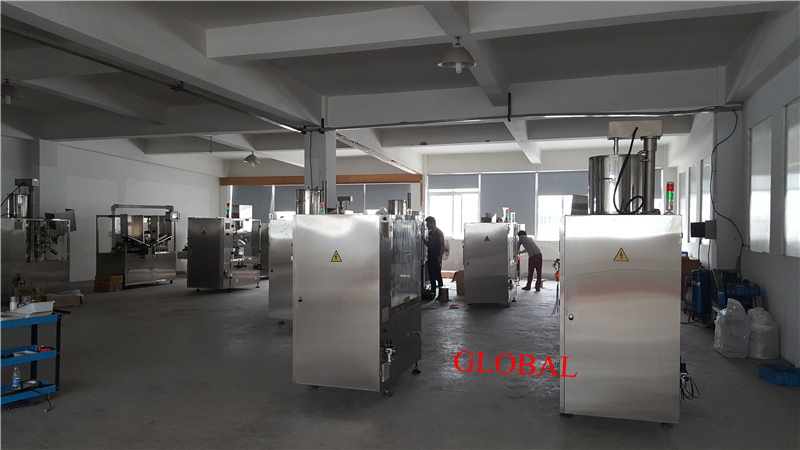
Single screw extrusion uses one screw within a cylindrical barrel to continuously push plastic through a constant profile die. Production rate is typically measured in mass per hour (lb/hour or kg/hour) and is controlled by the screw speed of the machine.
Most extruder products are produced using single screw extrusion. Parts such as window frames, house siding, and weather stripping, which have a constant profile, are generally produced by means of single screw extrusion. Due to such factors as the melt swelling as it exits the die, the die design for an extruder is critical. Great complexity is sometimes needed with an extrusion die in order to gain the correct profile.
The two largest industries for extrusion are pipe and tubing extrusion and film and sheet extrusion. There are many other industries that use extrusion to create their products though. Fiber extrusion, for clothing, coating extrusion, and blown film extrusion are just a few of the others.
Extrusion Single Screw Barrel,Single Screw Barrel,Single Screw Extruder Barrel,Single Screw Extruder Screw Barrel
Ningbo Jinyi Precision Machinery Co., Ltd. , https://www.jinyi-machinery.com